Siłownik pneumatyczny jest urządzeniem przekształcającym energię pochodzącą ze sprężonego powietrza do wytworzenia siły, która jest potrzebna do uruchomienia maszyny. Przedsiębiorcy korzystają z siłowników pneumatycznych m.in. w:
- urządzeniach przemysłu spożywczego i farmaceutycznego, np. w maszynach do pakowania i etykietowania produktów;
- automatyzacji linii produkcyjnych, np. w systemach transportowych i sortujących;
- maszynach do obróbki drewna, np. w piłach taśmowych i frezarkach;
- urządzeniach przemysłu chemicznego i petrochemicznego, np. w systemach dozujących;
- urządzeniach do obróbki metali, np. w tokarkach i wiertarkach.

Siłowniki pneumatyczne są w Polsce bardzo popularne z powodu niskiej ceny zakupu i dużej wytrzymałości na warunki pracy. Jednak przedsiębiorcy coraz częściej sięgają po alternatywy w postaci elektrycznych silników liniowych. Dlaczego tak się dzieje? Cena zakupu silnika liniowego w porównaniu do siłownika pneumatycznego jest przecież zdecydowanie wyższa. Poniesiony koszt zwraca się jednak w niecały rok. Dzieje się to za sprawą znacznie niższych kosztów eksploatacji podczas użytkowania silnika liniowego. Ponadto silniki liniowe cechują się podobnym do pneumatycznych poziomem wytrzymałości.
Ile wydasz na siłownik pneumatyczny i silnik liniowy w skrócie?
- Do badań przyjęliśmy maszynę, która podczas pracy przemieszcza poziomo masę o ciężarze 15 kg na drodze 800 mm w czasie 2 s. Maszyna pracuje 8000 h w roku, czyli wykonuje 14 400 000 cykli rocznie.
- Cena siłownika pneumatycznego waha się od 300 do 2 000 zł. Siłownik wybrany do naszych badań kosztuje ok. 700 zł.
- Roczny koszt energii przy wykorzystaniu siłownika pneumatycznego wynosi 17 540 zł.
- Cena elektrycznego silnika liniowego waha się od 5 000 do 40 000 zł. Silnik wybrany do naszych badań kosztuje ok. 14 000 zł.
- Roczny koszt energii przy wykorzystaniu elektrycznego silnika liniowego wynosi 273 zł.
Znacznie niższe koszty energii silnika liniowego sprawiają, że napęd elektryczny zwraca się w mniej niż pół roku. Po upływie tego czasu silniki liniowe pozwolą ci znacznie zaoszczędzić! Ponadto mniejsze zużycie prądu zdecydowanie zredukuje emisje CO2.

Dlaczego wybieramy silniki pneumatyczne?
- Szeroki zakres zastosowań, m.in. w przemyśle spożywczym, farmaceutycznym i transportowym.
- Niska cena zakupu.
- Działanie w szerokim zakresie temperatur.
- Odporność na wstrząsy i wilgoć.
Silniki pneumatyczne oferują dobrą jakość pracy w zamian za niską cenę zakupu. Ponadto są proste w obsłudze i nie wymagają prądu trzymającego, gdy są zainstalowane w orientacji pionowej. Rozwiązania pneumatyczne mają wiele zastosowań, dlatego korzysta z nich bardzo duża liczba fabryk.
Co wyróżnia konkurencyjne silniki liniowe?
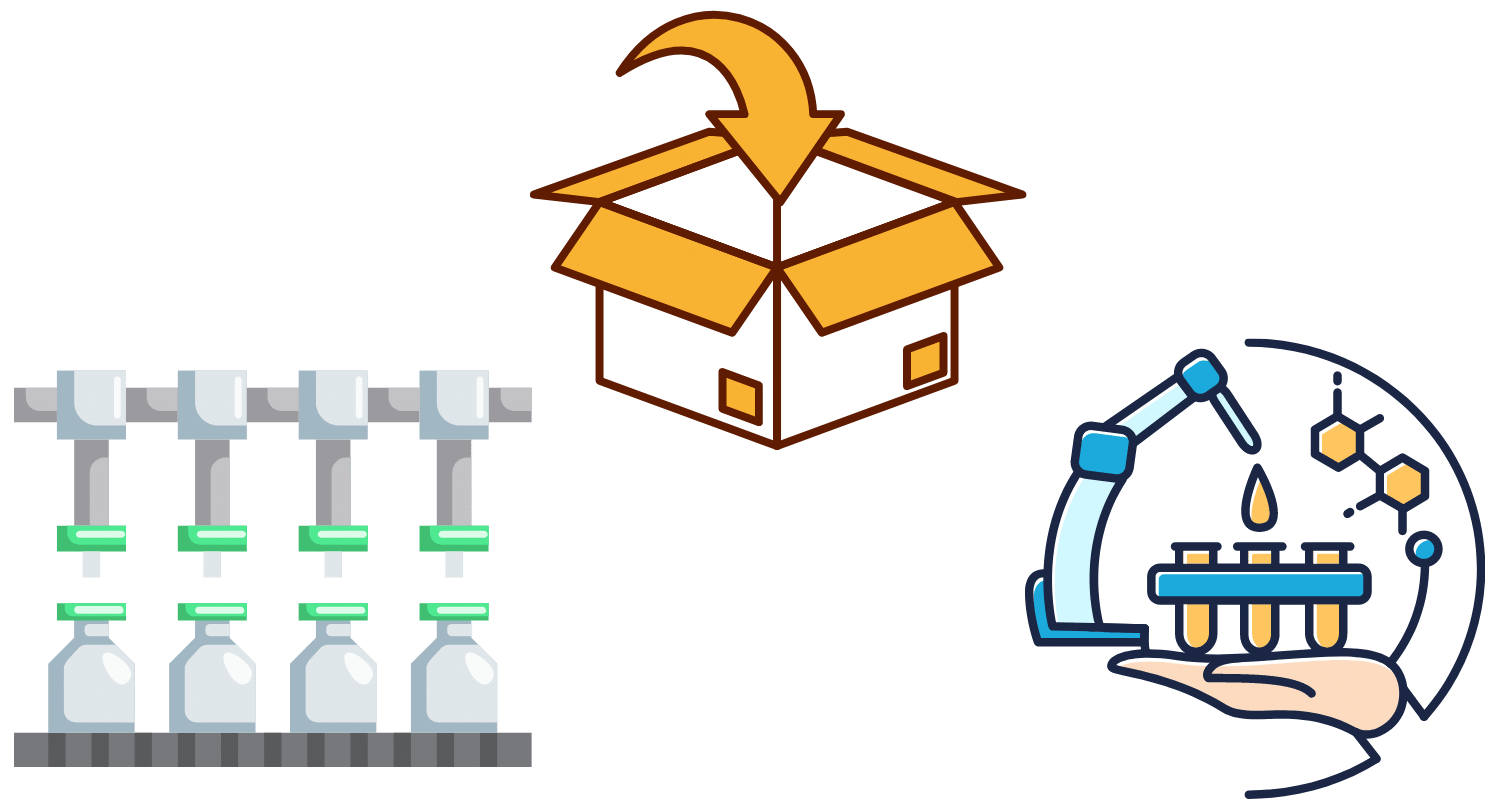
Szeroki zakres zastosowań, m.in. w:
przemyśle spożywczym, transportowym i farmaceutycznym
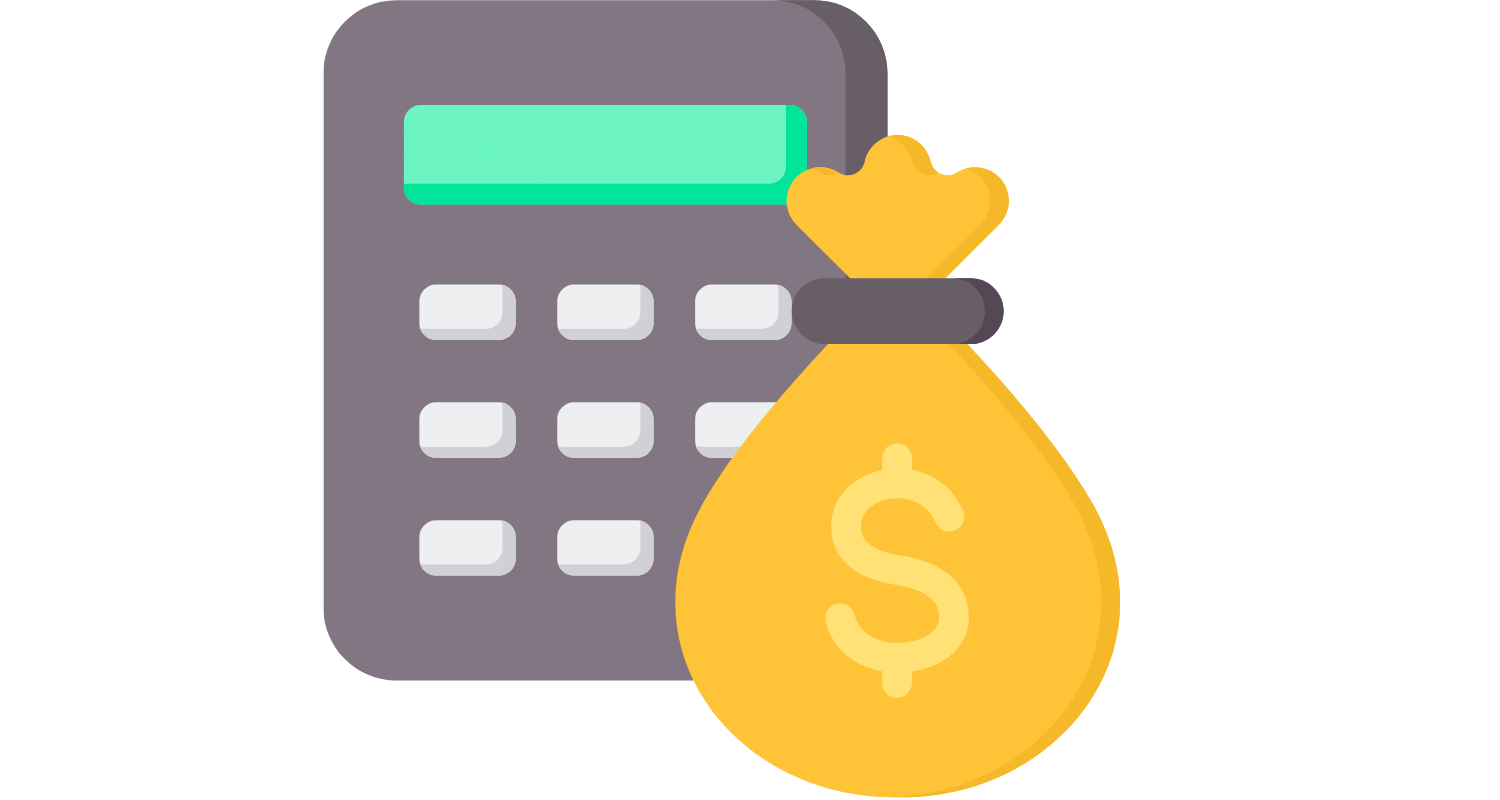
Wysoki koszt zakupu
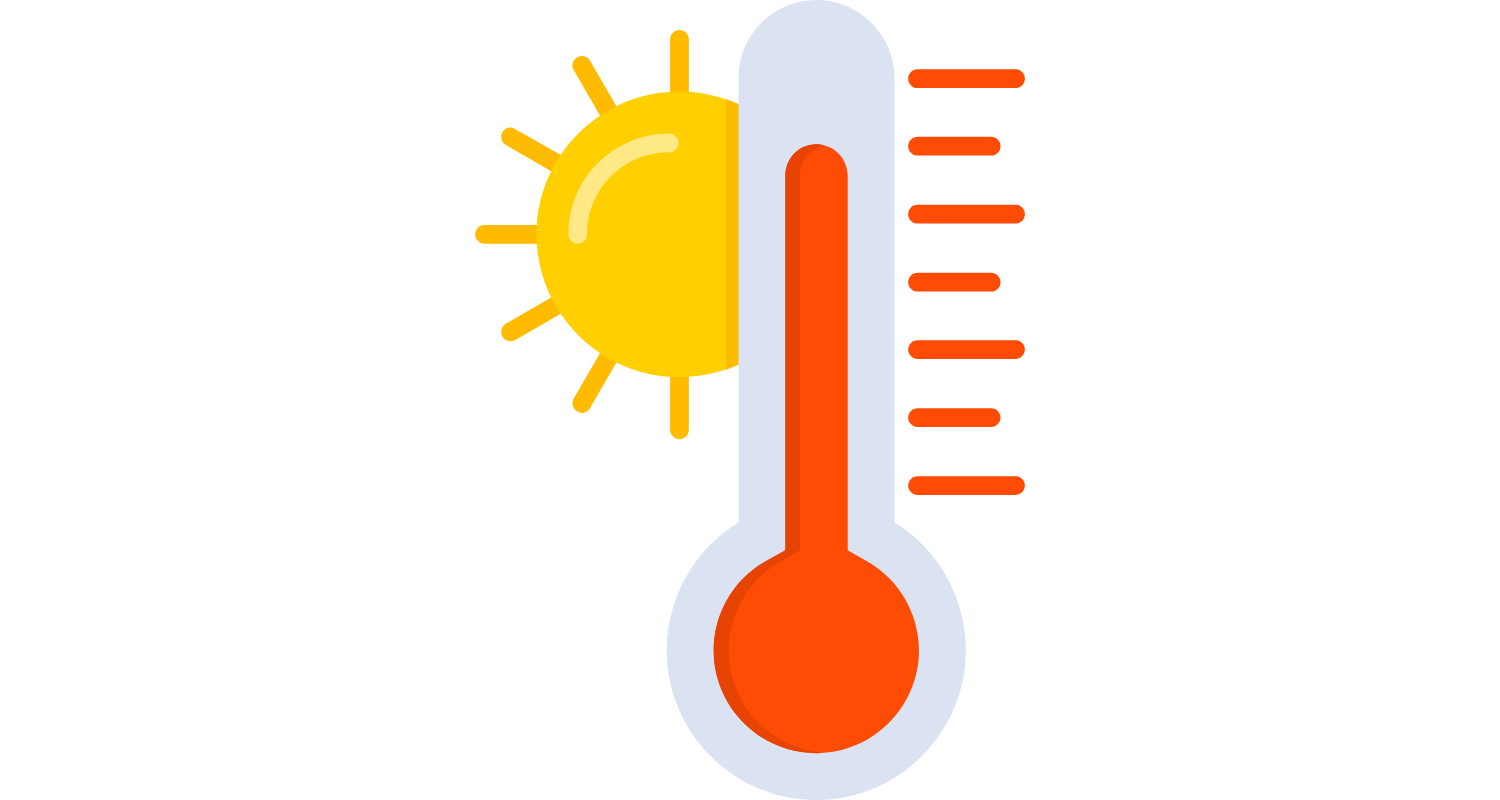
Działanie w szerokim zakresie temperatur
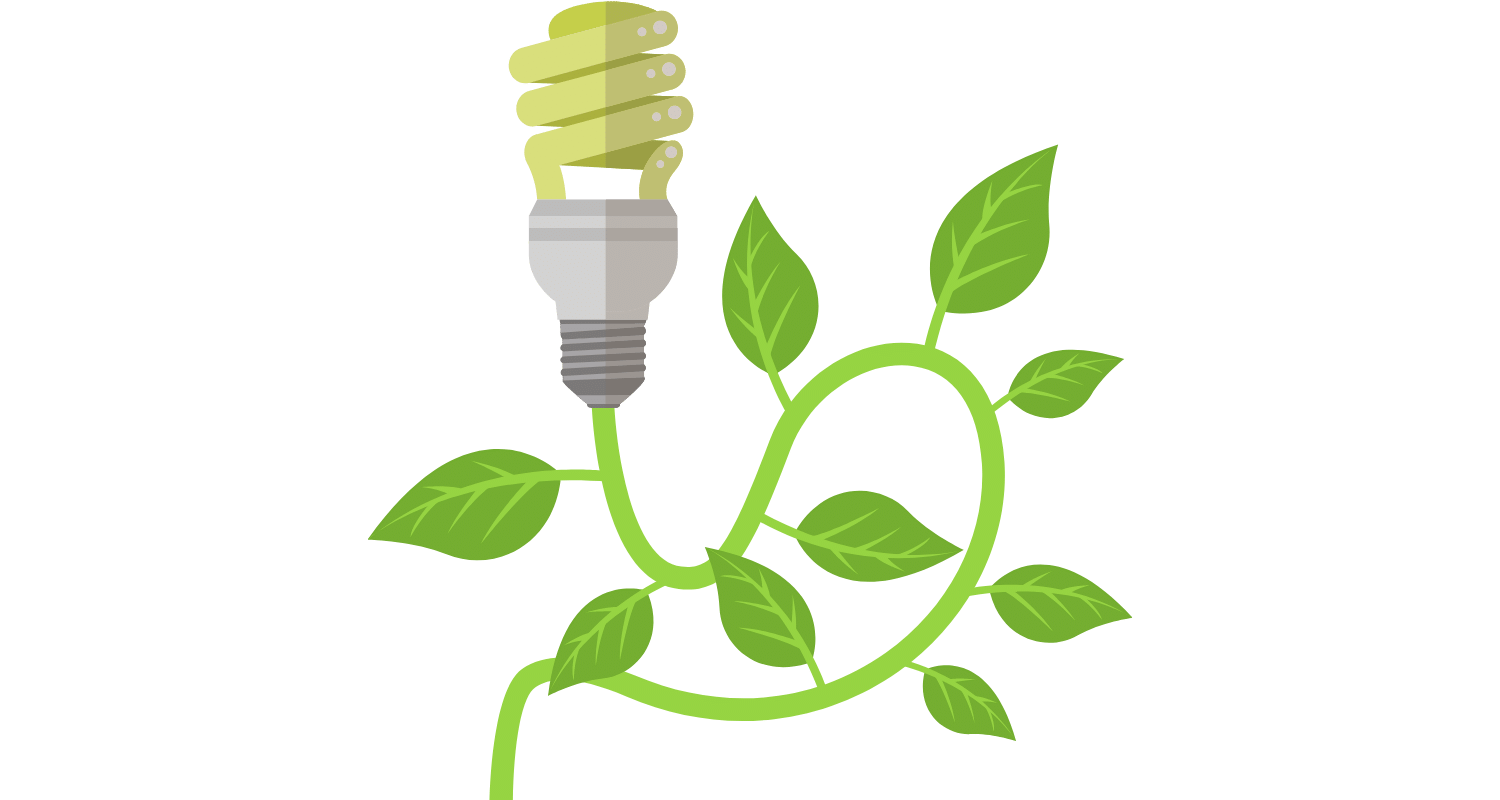
Bardzo niski koszt eksploatacji
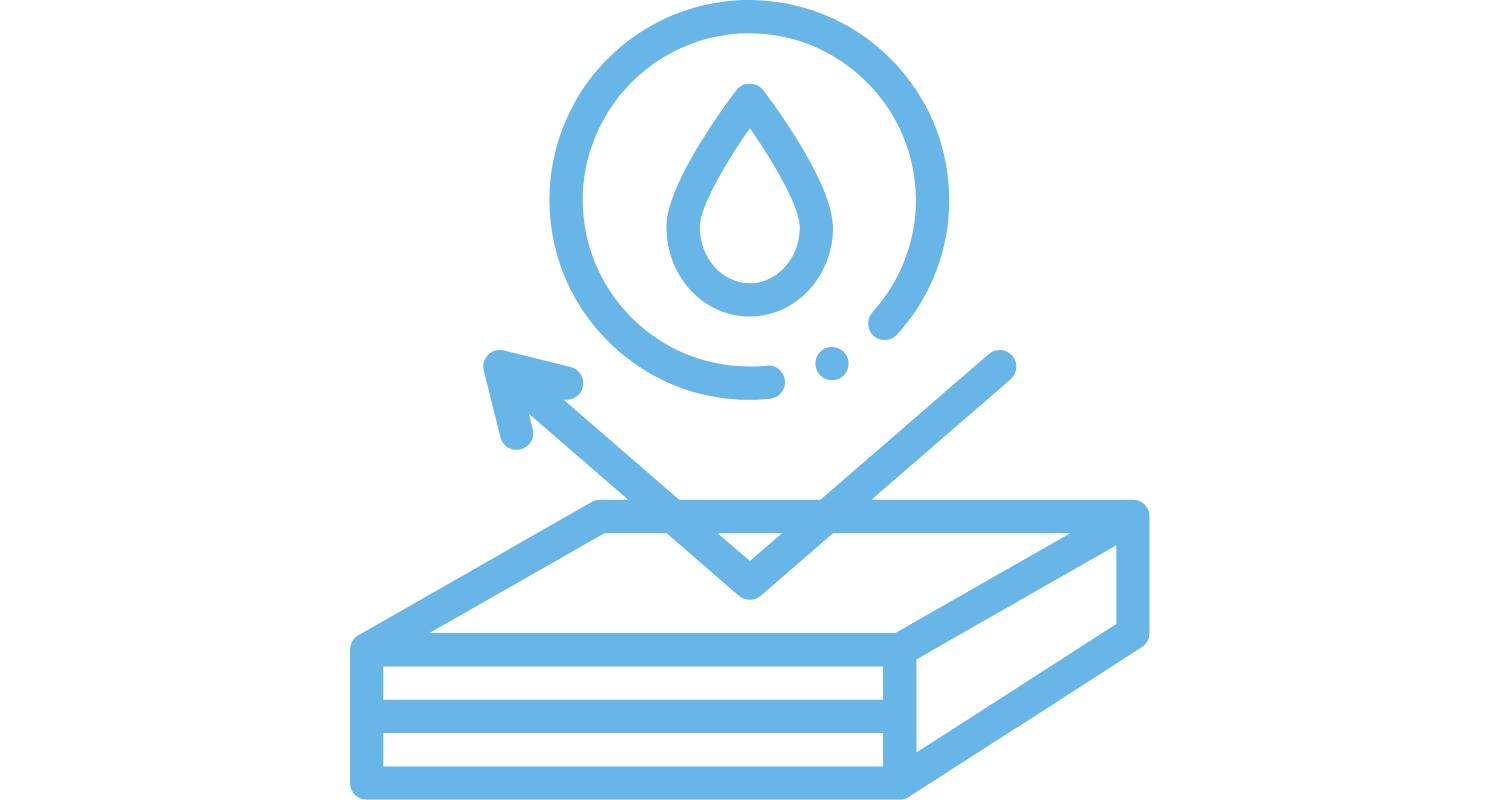
Odporność na wstrząsy i wilgoć
Wysoką cenę silników liniowych równoważy niski pobór energii elektrycznej. Poza tym precyzja, szybkość i wytrzymałość silników liniowych jest co najmniej porównywalna. Wbrew powszechnej opinii silniki liniowe charakteryzuje podobny zakres bezpieczeństwa w porównaniu do silników pneumatycznych. Przykładem tego są silniki liniowe ze stali nierdzewnej.
Koszty eksploatacji kompresorów powietrza
Zespoły kompresorów powietrza są powszechnie stosowane przez przedsiębiorstwa podczas transportu lub czyszczenia urządzeń. Duże zapotrzebowanie na sprężone powietrze przekłada się równocześnie na wzrost kosztów ponoszonych za wykorzystanie energii. Sprężone powietrze jest bowiem jednym z droższych źródeł energii.
Wysoki koszt sprężonego powietrza wynika z tego, że kompresory powietrza są w stanie przekształcić jedynie małą ilość energii wejściowej w użyteczną moc. Większość energii rozpraszana jest jako straty ciepła. Najnowsza technologia pozwala jednak na zwiększenie efektywności do 30% w zakresie wykorzystania energii przez sprężarki powietrza. Dalszy wzrost efektywności jest właściwie niemożliwy, ponieważ fizyczne limity zostały już praktycznie osiągnięte.
W sumie otrzymujemy wysoki koszt: silnika, sprężarki, strat ponoszonych podczas rozruchu i uruchomienia urządzenia, strat wynikających z nieszczelności systemów dystrybucji oraz strat wynikających z przesyłu sprężonego powietrza. Ostatecznie po dodatkowych stratach konwersji w siłowniku (bez optymalizacji) jedynie około 5% energii wejściowej jest dostępne jako moc użyteczna.
Optymalne zaprojektowanie systemu rur i elementów wykonawczych, szybkie wykrywanie wycieków oraz zastosowanie systemów rekuperacji ciepła mogą zwiększyć efektywność sprężarki. Ocenia się wówczas, że potencjalna oszczędność energii może wynieść między 20 a 40%.
Nawet jeśli te wszystkie warunki zostaną zrealizowane, to i tak pozostaje problem nieefektywnego wykorzystywania energii wejściowej przez systemy sprężonego powietrza, przy czym maksymalna sprawność całkowita możliwa do osiągnięcia wynosi 10%. Ponadto całkowity koszt pozyskania sprężarki okazuje się nieadekwatnie wysoki w stosunku do efektywnie wykorzystywanej energii. Podczas gdy około 10% całkowitego kosztu należy przeznaczyć na zakup urządzenia, a kolejne około 10% na konserwację jego systemu, to 70–80% kosztów całkowitych podczas wykorzystywania sprężarki stanowi zużycie energii.
W czasach rosnących cen energii i zwiększonej świadomości ekologicznej (zwłaszcza emisji CO2) coraz więcej firm stara się wyeliminować sprężarki powietrza ze swoich fabryk lub przynajmniej ograniczyć ich użycie do absolutnego minimum. Obecnie niemal bez wyjątku dostępne są alternatywy dla napędów stosujących sprężone powietrze. Dobrym zamiennikiem jest stosowanie uniwersalnych elektrycznych silników liniowych.
Założenia do obliczeń kosztów energii
Do porównania kosztów zużycia energii przez silniki w sprężarkach powietrza przyjęliśmy maszynę, która podczas pracy przemieszcza poziomo masę o ciężarze 15 kg na drodze 400 mm w czasie 0.5 s, zatrzymuje ją na czas 0.5 s, powraca na drodze 400 mm i ponownie zatrzymuje na czas 0.5 s.
Podstawą poniższych obliczeń jest artykuł producenta silników liniowych, który możesz zobaczyć tutaj.

Dla takiego przykładowego cyklu obliczyliśmy ilość potrzebnej energii dla siłownika pneumatycznego i silnika liniowego. Maszyna pracuje według podanego cyklu bez przerwy w systemie trzyzmianowym. Uwzględniając przerwy w pracy zakładu potrzebne ze względów serwisowych i socjalnych, przyjmujemy 8000 h pracy w roku. Cykl trwa 2 s (co daje 30 cykli na minutę), czyli w roku trzeba wykonać 14 400 000 cykli.
30 * 60 * 8000 = 14 400 000 cykli
Analizowany przez nas przypadek dotyczy wykonywania prostych ruchów prowadzonych od punktu do punktu pomiędzy dwoma pozycjami (w przypadku bardziej skomplikowanych ruchów opłacalność zastosowania silników liniowych będzie jeszcze większa).
Koszty energii dla rozwiązania z silnikiem liniowym
Dobór silnika liniowego
Program doborowy producenta dla przyjętego na wstępie ruchu wskazuje na użycie silnika o następujących parametrach: średnica statora 48 mm, średnica tłoczyska 28 mm, skok roboczy 400 mm, moc 48 W. Wybrany przez nas silnik liniowy kosztuje ok. 14 000 zł.

Obliczenia
Wymagany czas pozycjonowania 500 ms dla powyższego zadania osiągany jest przy przyspieszeniu 10 m/s² i prędkości jazdy 1 m/s. Czas przyspieszenia, w którym silnik liniowy wykonuje użyteczną pracę, wynosi 100 ms. Oznacza to, że efektywny pobór mocy ma miejsce podczas zaledwie 1/5 czasu pozycjonowania. W czasie postoju i podczas jazdy (ze stałą prędkością) silnik nie pobiera żadnej mocy poza tą, która jest potrzebna do pokonania tarcia. Energia kinetyczna, która powstała podczas hamowania, jest zamieniana w silniku na energię elektryczną i magazynowana w kondensatorach pośrednich serwosterownika, gdzie może być wykorzystana w kolejnym cyklu.
Przy założeniu 8 000 godzin pracy rocznie (praca na trzy zmiany) i cenie energii elektrycznej 0.71 zł/kWh (cena dla dużych przedsiębiorstw przemysłowych z uwzględnieniem podatków – wg EUROSTAT) całkowity roczny koszt energii wynosi 273 zł.
0,71 zł/kWh * 8000 h * 0,048 kW = 273 zł – roczny koszt eksploatacji silnika liniowego
Koszty energii dla rozwiązania z siłownikiem pneumatycznym
Dobór siłownika pneumatycznego
Jeżeli ładunek o masie 15 kg jest transportowany pneumatycznie z (maksymalną) prędkością 1 m/s (jak wymaga tego podany przykład zastosowania silnika), to należy zastosować siłownik pneumatyczny o średnicy tłoka 50 mm. Wybrany przez nas siłownik pneumatyczny kosztuje ok. 700 zł.

Obliczenia
W przeciwieństwie do silnika liniowego energia (sprężone powietrze) musi być doprowadzana przez cały czas trwania ruchu. Energia kinetyczna pochodząca z hamowania musi być również pochłonięta przez amortyzatory i nie może być od razu magazynowana na kolejny ruch.
Według karty katalogowej wybrany cylinder zużywa 0,02529 dm³ powietrza przy ciśnieniu 6 barów na każdy milimetr przesuwu w podwójnym skoku. Dla skoku 400 mm daje to zużycie 10,37 dm³ na cykl. Przy 30 cyklach na minutę siłownik pneumatyczny potrzebuje więc w sumie 150 000 Nm³ sprężonego powietrza rocznie przy pracy ciągłej (8 000 h/rok). Uwzględniając spadek ciśnienia, redukcję i straty wynikające z nieszczelności rzędu 25%, sprężarka musi sprężać i doprowadzać do rurociągu łącznie około 190 000 Nm³ powietrza.
10.37 dm³ * 14 400 cykli * 1.25 = 190 000 Nm³
Standardowa sprężarka (silnik o mocy 750 kW, wydajność 7 500 Nm³/h) może zużywać 0,130 kWh energii elektrycznej do sprężenia 1 Nm³/h przy ciśnieniu 6 barów, wliczając w to straty przy rozruchu i dobiegu oraz transport sprężonego powietrza.
Całkowity roczny koszt energii przy wykorzystaniu silnika pneumatycznego wynosi więc 17 540 złotych (0.71 zł/kWh * 0.130 kWh/m³ * 190 000 m³), czyli prawie 60 razy więcej niż w przypadku odpowiednika elektrycznego. Przy większej liczbie cykli, stosunek wykorzystania energii przez silnik pneumatyczny wypadłby znacznie gorzej w porównaniu do silnika liniowego.
Poza wyliczeniem czystych kosztów energii w kalkulacji kosztów całkowitych należy uwzględnić również koszty inwestycji i konserwacji. Testy wykazały, że łącznie stanowią one około 20% całkowitych kosztów eksploatacji, co daje nam łącznie koszt roczny pracy i konserwacji siłownika pneumatycznego wynoszący: 21 050 zł.
0.71 zł/kWh * 0.130 kWh/m³ * 190 000 m³ * 1.2 = 21 050 zł – roczny koszt eksploatacji siłownika pneumatycznego
Zredukuj emisję CO2, stosując silniki liniowe
Kolejną korzyścią z przejścia na elektryczny napęd liniowy jest olbrzymie zredukowanie emisji CO2. Energia 24.000 kWh, która w tym przykładowym wyliczeniu jest dodatkowo pobierana (w porównaniu do silników liniowych) przez siłownik pneumatyczny, daje w skali roku aż 12 000 kg CO2. Tym samym ilość emisji CO2 przemawia jednoznacznie za zmianą na elektryczne silniki liniowe!

Co wybierzesz? Oszczędności długo czy krótkofalowe?
Wysokie koszty stosowania przemysłowych siłowników pneumatycznych sprawiają, że przejście na elektryczne silniki liniowe opłaca się w coraz większym stopniu. Dotyczy to nawet prostych ruchów prowadzonych od punktu do punktu jedynie z dwoma pozycjami końcowymi, zwłaszcza w sytuacji, gdy ruchy wykonywane są regularnie w operacjach cyklicznych, a siłowniki pneumatyczne muszą być mocno przewymiarowane ze względu na prędkość i warunki obciążenia. W tym przypadku elektryczny napęd liniowy zwraca się w ciągu kilku tygodni.

Znacznie niższe koszty energii sprawiają, że napęd elektryczny zwraca się w mniej niż pół roku. Po upływie tego czasu dzięki silnikom liniowym możesz znacznie zaoszczędzić!
Szukasz oszczędności?
Skonsultuj zakup silnika z nami!
Newsletter
Podobał Ci się artykuł? Poinformujemy Cię o podobnych artykułach.
Dziękujemy!
Zostałeś zapisany do naszej listy sukskrybentów!
